Compton au boulot : Dave Lord et Kathy Chapdelaine
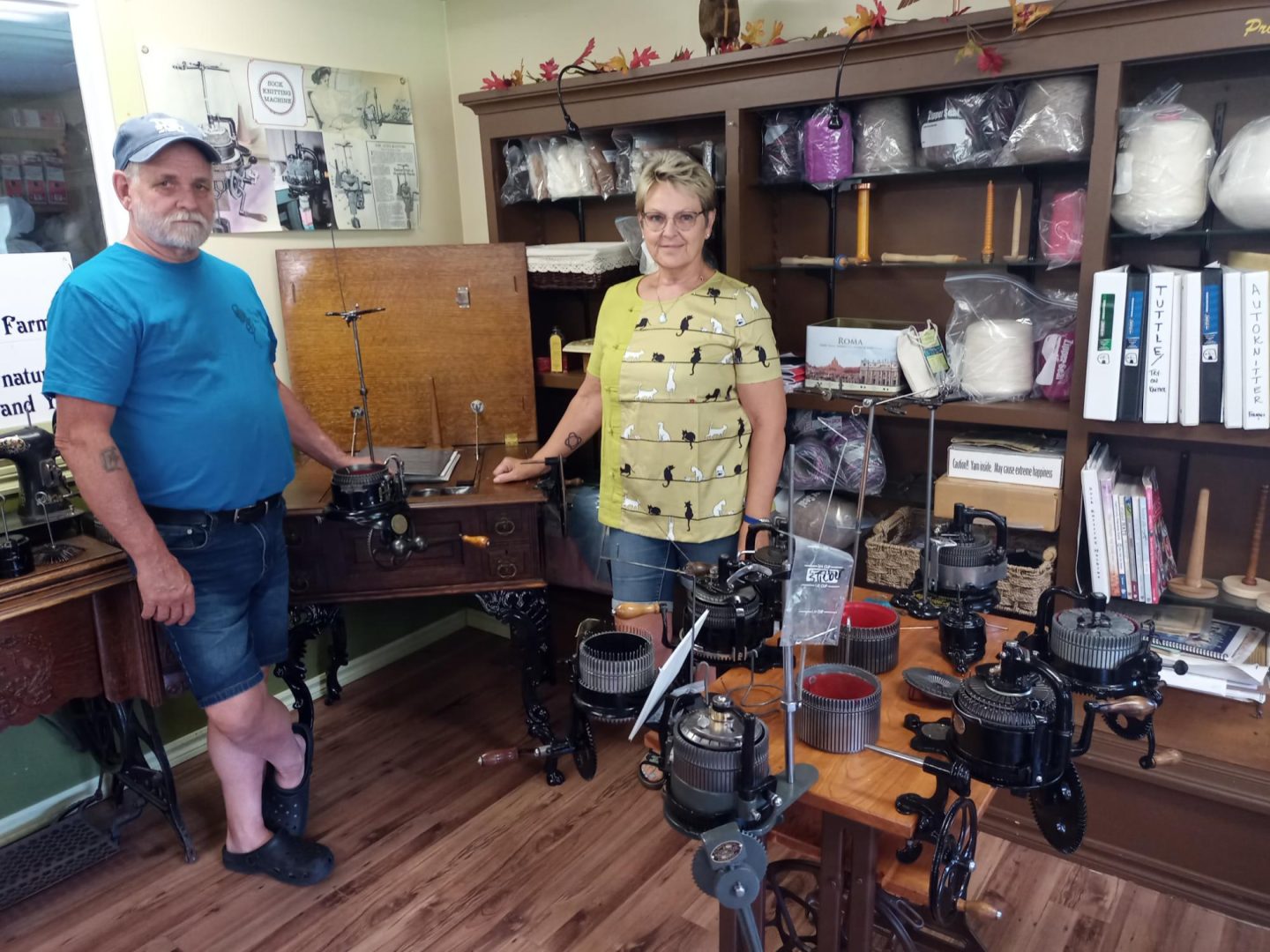
Un couple tricoté serré
Après avoir racheté la ferme de son père André Chapdelaine, Kathy Chapdelaine s’est dirigée dans la production de laine de différents animaux, dont les chèvres cachemires, les alpagas, les suris et différentes races de moutons. De son côté, son conjoint Dave Lord a travaillé pendant 35 ans comme directeur en recherche et en développement pour la compagnie NIEDNER à Coaticook, spécialisée dans le textile pour différents types de boyaux. À leur retraite, le couple comptonois a su combiner leurs expertises et leurs passions pour créer leur compagnie Tricoteuses Chambord CSM. Celle-ci comprend trois volets, la fabrication de tricoteuses neuves, la fabrication de pièces ainsi que la restauration de tricoteuses circulaires. Ainsi, ce patrimoine reprend vie au Québec, grâce à leur enthousiasme débordant.
D’où est venu votre intérêt pour les tricoteuses circulaires?
C’est pendant l’exposition annuelle des machines d’antan à Compton que nous avons vu pour la première fois une tricoteuse circulaire. Nous étions émerveillés par son fonctionnement simple, mais ingénieux. Dave a donc commencé à s’en procurer d’un peu partout. On s’est mis à collectionner différentes tricoteuses des 19e et 20e siècles, simplement parce qu’on les trouvait belles. La plupart du temps, il y avait des pièces brisées ou manquantes. Alors, Dave s’est mis à fabriquer des pièces et à restaurer les tricoteuses. Par la suite, notre amie Nicole Drolet, qui a fondé le regroupement Les Tricoteuses antiques du Québec, nous a contactés pour nous suggérer de fabriquer une machine complète. Dave a tout de suite accepté le défi. En 2017, il fabriquait sa première tricoteuse circulaire : la Chambord AccuKnitter 400.
Parlez-nous un peu de son histoire.
La tricoteuse circulaire se retrouve un peu partout dans le monde, surtout en Angleterre et aux États-Unis. Elle a évolué et s’est améliorée au fil des années. Au Canada, ce sont deux frères, Richard et Robertson Creelman, en Ontario qui se sont consacrés à leur confection de 1874 à 1926. Ils produisaient des machines pour d’autres compagnies qui les revendaient, comme l’entreprise de Pierre Théophile Légaré. Les gens pensent souvent que leurs machines étaient faites au Québec, car on retrouve le nom de P.T Légaré dessus, mais c’est faux. Cependant, c’est Légaré qui a vendu le plus de tricoteuses circulaires, des milliers et des milliers, en fait. Elles étaient reconnues comme les meilleures. En effet, elles perdurent de par leur qualité.
Que fait-on avec ce type de tricoteuse?
On peut fabriquer toutes sortes de produits comme des bas, des tuques, des foulards, de la dentelle, des mitaines, des bandeaux, des panneaux pour des combines ou autres projets de tricot, etc. La tricoteuse fait la base, puis on finalise à la main. Quelqu’un qui a de l’expérience peut fabriquer une paire de bas en moins de 45 minutes.
L’atelier de travail Quelques articles Une tricoteuse
Quelles sont vos tâches respectives dans l’entreprise?
Moi, je m’occupe du service clientèle et de tout ce qui touche la comptabilité. Je fais aussi les emballages pour les expéditions de colis. Je réponds aux courriels et note les commandes. Mon conjoint s’occupe de la fabrication des machines et des pièces ainsi que de leur restauration. Les gens nous envoient leurs vieilles tricoteuses pour que Dave puisse les remettre à neuf. Avec le jet de sable, il enlève la rouille pour revenir au fond de fonte. Il applique une peinture en poudre électrostatique et il polit les pièces. On reçoit aussi beaucoup de commandes de pièces. Lorsqu’on reçoit une demande pour une pièce spécifique à un de nos 47 modèles, Dave va démanteler une de nos machines pour modéliser la pièce manquante sur la tricoteuse à réparer. Il va faire le dessin, puis reproduire la pièce. Ensuite, c’est envoyé au client qui pourra réutiliser sa machine. Ce sont des modèles qui n’existent plus, donc impossible d’avoir les pièces ailleurs.
Quelles sont les particularités de vos tricoteuses Chambord AccuKnitter 400?
De nos jours, il reste six producteurs de tricoteuses circulaires dans le monde, mais ce sont toutes des usines. Certaines les fabriquent en aluminium, alors que les anciennes étaient en fonte, donc plus résistante. De notre côté, nous achetons d’une fonderie locale à Waterloo le matériel de base pour cylindres et côteleurs en fonte. Ensuite, avec des machines programmées, Dave grave les détails, dont le nombre de rainures désirées sur le cylindre. C’est ce qui détermine le nombre de mailles. Le reste des pièces est en acier, dont les aiguilles à clapet que nous faisons venir de Corée. Lorsqu’ils commandent, nos clients peuvent choisir la couleur et le nombre d’aiguilles. Aussi, chaque machine a une plaque en laiton où l’on grave un nom ou un message choisi par l’acheteur. C’est artisanal et personnalisé.
Y a-t-il une forte demande?
Oh, oui! C’était un projet de retraite au départ, mais on peut dire qu’on a été victime de notre succès. En fait, on ne fournit pas à la demande! On a 1 500 clients à travers le monde. Dave a vendu 115 machines neuves, dont certaines au Japon et en Allemagne. Cependant, notre objectif premier demeure de sauver ce patrimoine historique. Tant d’entre elles ont été envoyées à la ferraille, c’est vraiment dommage. On veut donc prioriser la fabrication de pièces et la restauration. La pandémie, le bouche-à-oreille, puis les réseaux sociaux ont vraiment offert un second souffle à cette belle et pratique machine. Malheureusement, les acheteurs de machines neuves se retrouvent dans une longue liste d’attente. On garde quand même espoir en espérant bien trouver une relève.
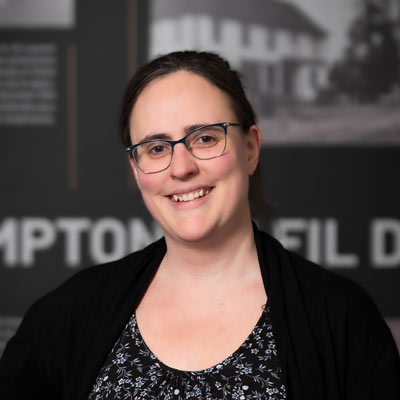